QUALITY CONTROL
QUALITY POLICY
Canadian united building Co. endeavours to provide high quality products at affordable prices, designed to achieve complete customer satisfaction. All functions are geared to meet the requirements of the quality management system. A good marketing department helps in understanding customers’ needs better resulting in effective execution of jobs. We strive to remain in the organisation of First Choice in all our products & Services.
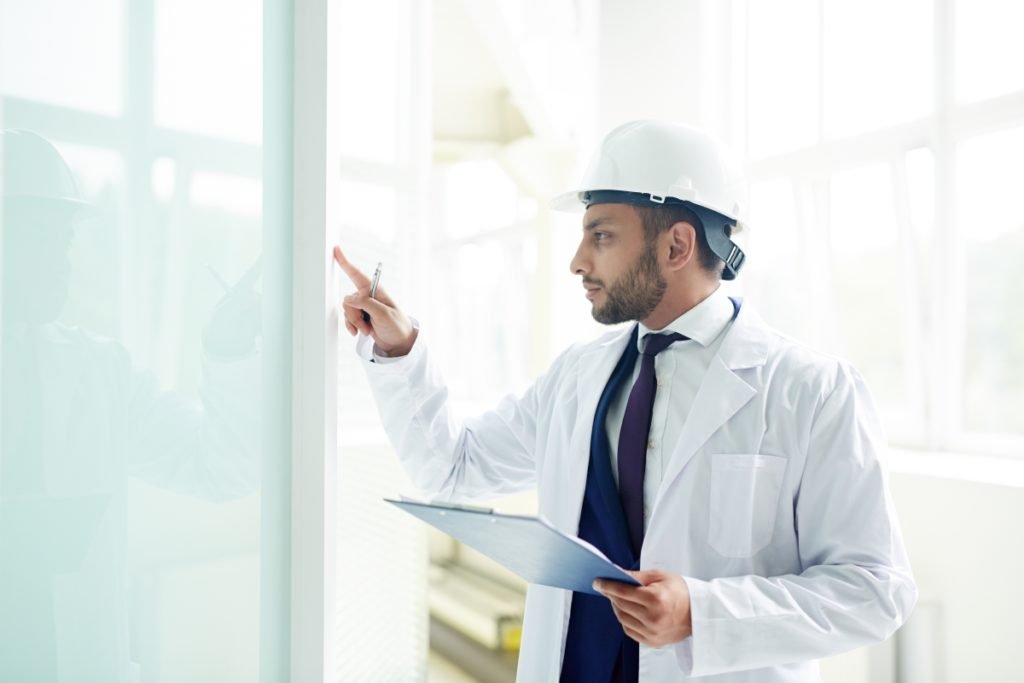
QUALITY OBJECTIVES:
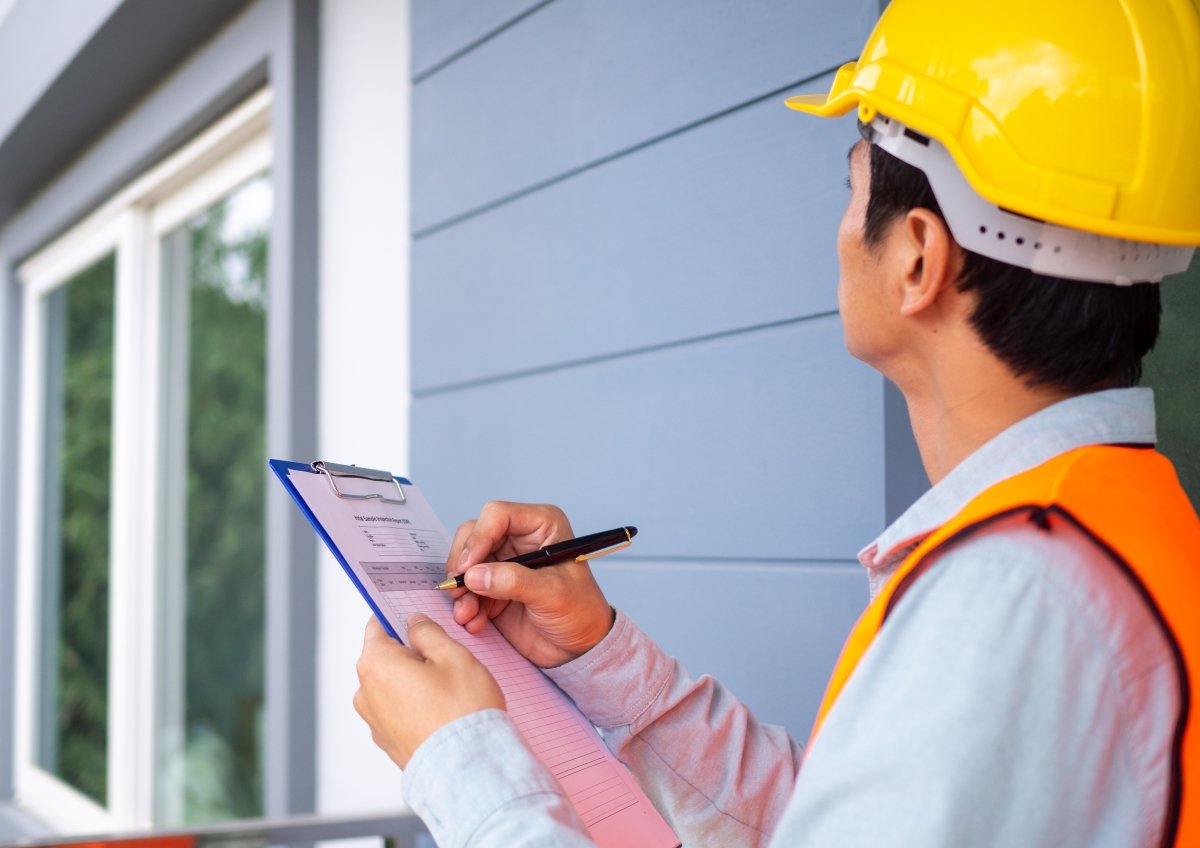
- Establish and monitor at all stages quality system based on the international guidelines.
- Regular review of our product and services, feedback from working manpower system to deliver the improved quality products.
- Offer our clients excellent services, innovative product usage in end products with value added to deliver to them for mutual benefit of both.
- Educating and creating awareness of demonstration vision, professionalism, transparency and integrity in conduct of our business and product service.
- Vouch on disciplined growth and reasonable profitability during operation of business in sound and healthy finance base.
- Encouraging /motivating self-thinking and dedication among human resources to protect the management interests in accordance to the implementation of government policies and objectives transferred in the trade circle.
- Contribute the eligible share from the market to the management from the community of trade activity.
Quality Implementation:
The manufacturing process is monitored at all stages to ensure that quality as well as safety procedures are followed. Efficient utilization of material and manpower is achieved by maintaining high standards in quality control. Timely completion and delivery is also achieved within the constraints of cost and quality.
After a contract is signed, the client is briefed on the types of materials being used and samples of the major materials for the project are made available to the client. On receipt of the client’s approval, the materials are procured and subjected to stringent quality checks. Even the slightest variation in quality of materials is not tolerated, as material is the most important element of production.
A detailed job instruction is prepared by the Department and sent to the Works along with a copy of Bill of Quantity (BOQ), which specifies the type, quality and quantity of materials to be used. This ensures that the Stores issue the right material to a particular job. The Machines are routinely checked so that they are fit for use and the Works Supervisor scrutinizes the BOQ for doubts if any. Then the job commences on issue of his instructions. He ensures that accuracy is maintained and that defective wood works are discarded while following the actual design and specifications. The finishing section follows the detailed instructions on the specific type of finishing to be done and maintains a separate record on the time taken for sanding, painting, etc.
In Steel Fabrication jobs, the quality of steel members and specification required are verified before they are issued to jobs. The Section Supervisor ensures that the quality of work is proper. The above detailed procedure followed by the company assures the quality of the final product.
Quality Control:
Stringent quality controls and checks are carried out at the works to ensurethat the products meet the required high standards. All workers are madeaware of their responsibilities in maintaining the required standards in qualitythrough quality training and guidance. Quality audit is undertaken as anintegral part of the manufacturing process beginning from the raw materialstage to the finished product stage.